Stela Belt Dryer BT 8400
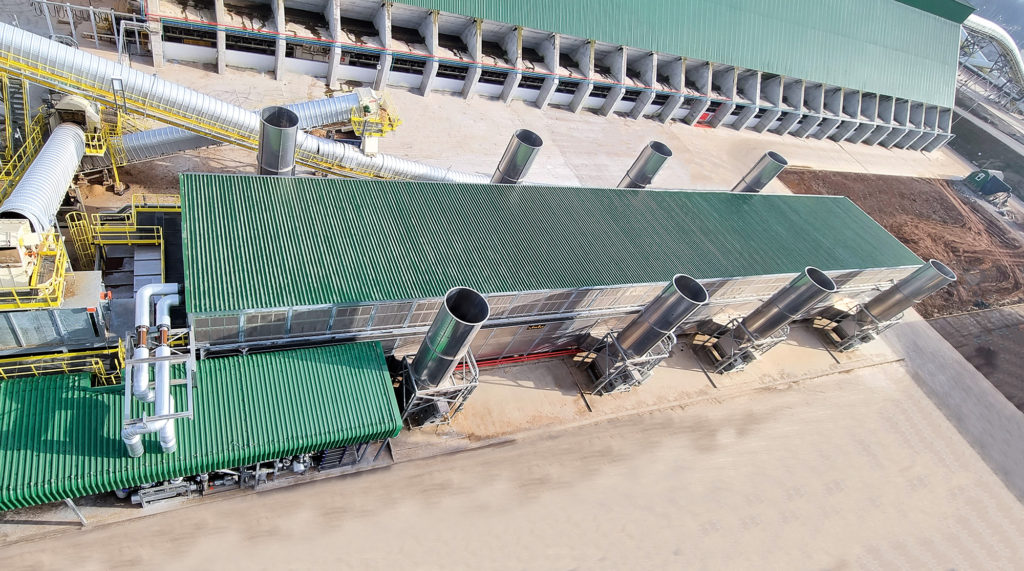
Latest news
B&W Enters Kiewit, Fidelis Biomass Project
Babcock & Wilcox is partnering with Kiewit Industrial to deliver Fidelis New Energy’s planned net-negative carbon impact biomass power plant at the Port of Greater Baton Rouge, La. The 200 MW electricity plant will be the largest of its kind in the world, according to the participants…
Enviva, MOL Drybulk Debut New Partnership
Enviva and MOL Drybulk Ltd., a subsidiary of Mitsui O.S.K. Lines Ltd., a leading global marine transport group, announced they have signed an additional memorandum of understanding to deploy an environmentally friendly bulk carrier (“EFBC”) to reduce the greenhouse gas (“GHG”) emissions in the ocean transportation of sustainable wood pellets and biofuels…
Drax Participates In Parade To Celebrate ‘Pen Friends’
To celebrate the end of a successful first year of the “Pen Friends” program, Drax employees took part in a mobile parade where they decorated their cars and visited Morehouse and Delta Elementary Schools to meet the pupils they had been corresponding with. Volunteers also presented their Pen Friends with small…
Forest Service Reveals Immediate Forest Plans
U.S. Forest Service reported it sold 2.87 billion BF of timber sales (compared to the agency target of 4 billion BF) in fiscal 2021, a decrease from 3.2 billion BF in FY 2020, according to the agency’s Fiscal Year 2023 Budget Justification document. The sold volume was valued at $197 million…
Find Us On Social
Subscribe to Our Newsletter
Wood Bioenergy News Online hits the inboxes of subscribers in the wood-to-energy sectors.
Subscribe/Renew
Wood Bioenergy is published and delivered worldwide 6 times per year. Free to qualified readers in the U.S. Subscribers outside the U.S. are asked to pay a small fee.
Advertise
Complete the online form so we can direct you to the appropriate Sales Representative.